|
您现在的位置 > 技术资料
拉深加工质量缺陷的原因分析及对策 |
发布时间:2022/7/4 |
拉深加工质量缺陷的原因分析及对策
在拉深加工过程中,对遇到的问题应仔细观察,细心分析,从拉深加工工艺、所操作拉深模各零部件的结构、拉深材料等众多的影响因素中找出具体的原因,并采取正确的处理措施。以下通过几个实例进行分析说明。
1.制品的外形及尺寸发生变化
拉深模工作一段时间以后,制品经检查发现其形状和尺寸发生了变化。根据生产经验可从以下方面对其产生的原因进行分析,检查。
(1)检查压边圈在工作时是否有不平现象 如果压边圈不平整,会使板料在拉深过程中进入凹模的阻力不均匀,致使变形阻力小的那一面侧壁低而厚,而阻力大的那一面侧壁高而薄,如图2所示。
调整修复措施是:检查凸模与凹模的轴心线是否由于长期振动而不重合,压边圈螺钉是否长短不一,凹模的几何形状是否发生变化或其四周的圆角半径由于磨损严重而不一致,并根据不同情况加以修整。
(2)检查凹模圆角半径是否均匀 如果凹模圆角半径由于长期磨损而变得不均匀(特别是拉深盒形件),拉深时板料各部位流动和变形情况就不一样,所以在拉深件的边缘上常常伸出大小不均的余边,使制件的边缘参差不齐,厚薄不均,或者使制件局部产生细小的褶皱,影响制件质量。对策是修磨凹模圆角半径,使之保持均匀。
(3)检查凸模与凹模的中心线是否在共线如果凸模与凹模的中心线不共线,如图3所示,则凸模与凹模间隙不均,这样在制件侧壁上就会出现一边高一边低,一边薄一边厚的加工缺陷,有时制品还会在间隙小的一边出现破裂。产生这种现象的主要原因是模具的定位部分产生偏差,如定位销孔的孔距或孔径由于长期振动而变化等。对策是对冲模进行重新装配与调整,使之恢复到原来的状态。
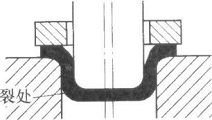
图3凸模与凹模不同心时所产生的制件缺陷
此外,还应检查板料定位板的中心是否与凹模中心重合。若两者不同心,也会产生同样的问题,即由于板料的滑动变形量各不相同,一边多而另一边少,则制品也将产生一侧高一侧低形状,必须给予调整或更换定位板备件。
(4)检查凸模在使用过程中是否由于松动而导致冲压件歪斜,假如凸模在冲压时歪斜进入凹模,则凸、凹模各处的间隙都不一样,就会使制件壁的变形不一致,产生一边高一边低,一边薄一边厚的现象,严重时还会被拉裂,若经检查产生的缺陷仅因凸模歪斜,而其他尺寸没问题,则可以用凸模的工作柱面作为基面进行找正,把定位底面修磨到同它垂直;若尺寸还有问题,则在保证定位底面同工作柱面垂直后,还需修整其尺寸。
造成凸模与凹模中心线不平行的原因还可能是凹模的定位底面同工作柱面不垂直。要避免这种缺陷,在使用机床磨削或钳工进行修整时,应当用千分表或直角尺来校正,使孔壁同顶平面保持垂直,如图5所示。
修复可采用先用凹模的工作柱面作为基面进行找正,把定位底面修磨到同它垂直后,再以定位底面为基面在平面磨床上磨削另一平面的加工方法。
(5)检查压边圈与凸模或凹模的间隙一般情况下,压边圈(压料板)在冲模中是套在凸模(在复合模中是放在凹模孔内)上沿着凸模移动的,它的位置并没有固定。若压边圈与凸模的间隙过大时,也会造成彼此间偏心,使压料不正而射起压办不均匀,造成板料移动和变形不一致,形成上述同样的加工缺陷。其对策是对压边圈与凸模或凹模的间隙进行调整,使之各边间隙在0.01~0.02mm。若压边圈(压料板)磨损太大,应更换新的备件。
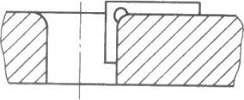
图5 凹模孔垂直度的检查方法
(6)检查冲模各部件装配的牢固性这是因为冲模零件在冲模中的准确位置是由定位销(圆柱销)和螺钉来保证的,而紧固后的各零件在冲模工作一段时间后,会因振动而失去原有的牢固性,致使各个零件间相对位置发生变化,特别是凸模与凹模位置的变化,不仅冲不出合格的制品来,有时还会使模具裂损而报废,出现不必要的事故。所以冲模在使用一段时间后,维修工必须对其进行修整和检查。经常保持销钉及螺钉的定位和紧固作用。
2.拉深件出现起皱、裂纹或破裂现象
在拉深件的拉深过程中,制品起皱、裂纹或破裂是经常发生的。可以从以下方面对其产生的原因进行分析,检查。
(1)检查压边圈的压力 压边圈的压力过大会增加板料在隧模上的滑动和变形阻力,使板料承受凸模的强烈拉力而发生裂纹。这种故障开始时材料仅发生变薄的情况,当拉力超过了材料的抗拉强度时,就形成了韧性裂口。对策是减少压边圈的压料力,如减少压料面积、设置限位柱减小压紧程度等,对气垫压料,可将气垫的单位压力减小一些。
(2)检查凸模与凹模的圆角半径应检查凸模与凹模的圆角半径是否受到损坏或磨损,当圆角磨损后变大时,所需要的拉深力变小,板料外缘受压部位减少而圆周方向上受压缩范围增大,致使制品拉成后所留下皱纹的周边加大。当圆角半径变小时,板料所产生的内应力增大,又会造成制品的破裂或整个底部被冲掉。特别是在拉深矩形盒零件时,它的变形主要集中在四个角处,其凸、凹模的圆角对产品质量有很大的影响。对策是修复凸、凹模的圈角半径,尽量使其大小合适。
(3)检查凸、凹模的间隙拉深模问隙对制品质量有很大影响。合理的间隙值是比料厚公称尺寸稍大一些,这样能使多余的材料逐渐向上移动,不至于将制件拉破、拉皱,或使制品产生裂纹。当间敲变化时,如凸、凹模由于振动影响位置发生变化,造成一边间隙大,一边间隙变小,则间隙过小的一面制件会被拉毛,壁厚变薄,且使拉深力突然增大,从而增加了材料的应力,结果会使制品的底边被拉裂,并加速了凹模的磨损;间隙过大的一面就会发生褶皱或使制件壁倾斜,造成底小口大。对策是调整凸、凹模,保证其间隙均匀,若经磨损阔变大无法修复则必须更换新的备件。
(4)检查凸、凹模的表面质量 检查凸、凹模的表面质量主要应集中在检查凹模溷角部分及圆角部分附近的质量,除了要求有足够的强度外,其表面必须光洁,因为这是板料产生最大变形的区域。若冲模在使用一段时间后,由于表面质量降低,则凹模面就会粘附一些碎片或被拉成凹坑,不但会影响制品的表面质量,还会使毹。臻被拉袭或拉皱。对策是模具在使用一段时间后,必须对凸、凹模表面进行抛光处理。
(5)检查压料板(压边圈)是否平整压料板(压边圈)应平整,表面应光滑,否则板料在拉深过程中流动会不均匀,压料板失去压料作用,致使制品起皱。压边圈在使用一段时间后应及时取下磨光。
(6)检查凸、凹模的中心是否在同一轴线上应检查凸、凹模的中心是否在同一轴线上,凸模工作时是否与凹模垂直。出现问题时的对策是调整或修复凸模与凹模。
(7)检查压力机滑块的运动速度应检查压力机滑块的运动速度是否符合冲压生产工艺的要求。对拉深工艺来说,若滑块速度过高,易引起工件的破裂。拉深工艺的合理速度范围如表7所示,进行拉深加工的压力机,滑块速度不应超过这个数值。
表7拉深工艺的合理速度范围 (单位:mm/s)
拉深材料 | 钢 | 不锈钢 | 铝 | 硬铝 | 黄铜 | 铜 | 锌 | 最大拉深速度 | 400 | 180 | 890 | 200 | 1020 | 760 | 760 |
3.制品表面出现擦伤
在拉深件的变形过程中,由于毛坯要逐渐滑过拉深凹模圆角部位的变形区,拉深件侧壁都将出现滑动的痕迹。这是一种具有金属表面光泽的细微划痕,这种细微划痕对拉深件来说是很普遍存在的,也是允许的,通过擦拭或简单的抛光便可消除。若出现严重划痕或划伤,则称为制品表面擦伤,这是不允许的。可以从以下方面对擦伤产生的原因进行分析和检查。
(1)检查凸、凹模的工作状况应检查凸、凹模工作部分是否有裂纹或损坏,表面是否光洁,这是因为拉深毛坯在通过这些损伤表面时将不可避免地出现严重划痕。出现问题时的对策是修磨或抛光损伤表面。
(2)检查凸、凹模间隙应检查凸、凹模是否存在间隙不均匀,或研配不好,或导向不良等问题,因为出现这些问题都可能造成局部压料力增高,使侧面产生局部接触划痕或变薄性质的擦伤。对策是调整凸、凹模的间隙使其均匀,保证凸、凹模工作部位的研配质量,保证凸凹模工作表面低的表面粗糙度值和尺寸的一致性。
(3)检查所加工的毛坯表面质量应检查所加工的毛坯表面是否清洁,检查毛坯剪切面的毛刺和模具及材料上的污物或杂质是否清除,这些因素对制品表面擦伤的产生有直接影响。对策是清洁毛坯表面,清除毛坯剪切面的毛刺和模具及材料上的污物或杂质。
此外,正确地选用模具材料并确定其热处理硬度,也是减轻拉深擦伤的一个有效措施。一般来说,应选用硬材质的模具来加工较软材料,选用软材质的模具来加工硬材料。例如,加工拉深铝制件时,可采用热处理硬度较高的材料来制作模具,也可用镀硬质铬的模具;而加工不锈钢制件时,则可采用铝青铜模具(或用铝青铜镶拼覆盖的结构形式),这样可以收到较好的拉深效果。另外,在拉深时采用带有耐压添加剂的高粘度润滑油,或对毛坯涂表面保护涂层(如不锈钢采用乙烯涂层等),效果也较好。
4.制品表面出现高温粘结
拉深件表面出现的另一种缺陷是摩擦高温粘结,即在侧壁的拉深方向上产生表面熔化和堆积状的痕迹。这种痕迹开始出现时,会在模具或制件表面产生一两条短的、浅的线痕,往往呈条形或线形,如不及时消除将很快出现更多、更深的线痕直至模具不能使用。这不仅对零件表面质量造成损害,严重时甚至引起生产故障。这种情况最易发生在凹模的棱边部位,也就是凹模的圆角部位。因为在拉深过程中,这些部位的压力很大,因而滑动面的摩擦阻力很大,会产生甚至可能达到1000度左右的高温,从而导致模具表面硬度降低,并使被软化的材料呈颗粒状脱落,局部熔化粘结在模具上而拉坏制件。它类似于机械加工中在刀具工作表面产生的拉削瘤所造成的破坏。
对于摩擦高温粘结,必须充分重视。用硬而厚的难加工材料(如钢、不锈钢等)进行复杂形状且变形程度不大的拉深最容易发生这类问题。因此,应在拉深工作开始前就进行充分研究并采取预防措施,当发生问题时再进行修复或解决就比较困难了。
凹模材料及其热处理和凹模表面的加工质量是影响摩擦高温粘结的主要因素。因此,对于在拉深过程中容易发生高温粘结的模具,应选用材质较好的合金工具钢、优质模具钢或硬质合金等材料铡造,并应执行正确的热处理工艺,以获得材料良好的组织、足够的硬度和刚度。这一点是极为重要的。对于凹模的边棱、圆角表面应进行仔细的精加工,使之有利于材料的滑动。对于摩擦高温粘结特别严重的模具部位,应考虑采用镶拼式结构,以便于及时更换和维修。
此外,在拉深硬而厚的难加工材料时,应在凹模和材料的接触表面合理、正确地使用润滑剂。
5.模具磨损严重
模具磨损严重是指模具的正常使用寿命大大缩短的非正常磨损,且导致拉深件质量和精度严重降低。
(1)磨损部位拉深模产生磨损的主要部位如下:
1)在毛坯材料流入较多和流动阻力较大的地方,如凹模圆角处、凹模表面和拉深凸肋处等。这些部位由于表面压力大,模具的磨损也就大。模具在这些部位的磨损和粘结是造成划痕和异物凸起等问题的主要原因。
2)在板厚增加较大的部位磨损也较大。板厚加大,虽然在这个拉深变形区域不会产生皱纹,但该部位的表面压力就要增加,同样容易引起粘结和磨损。
3)在形成褶皱的部位,模具的磨损也增加。皱褶不同的高低部位,对凸模和凹模的局部表面都增加了表面压力,进而造成磨损。通常,容易发生褶皱是因为拉深深度过大或材料流动量大,这一因素和皱褶的共同影响,将使磨损变得更加严重。
(2)措施为减轻模具磨损通常采取以下措施:
1)应根据板料变厚的实际情况取凸、凹模的阎隙值,这样可以防止局部压力增强,以减少粘结和磨损。
2)正确润滑。在粘度不高的润滑油里添加耐高压的添加剂,对减少模具磨损能起到很大的作用。此外,正确和合理的润滑也改善了拉深条件,有时还能减少制件起皱现象。
3)使用耐磨性好的材料,并进行正确的热处理,使模具具有高的硬度和耐磨性。
4)消除皱褶。通过消除皱褶来减少由于皱褶引起的磨损,如改善凹模表面的形状和精度、合理地布置拉深肋等。
|
|